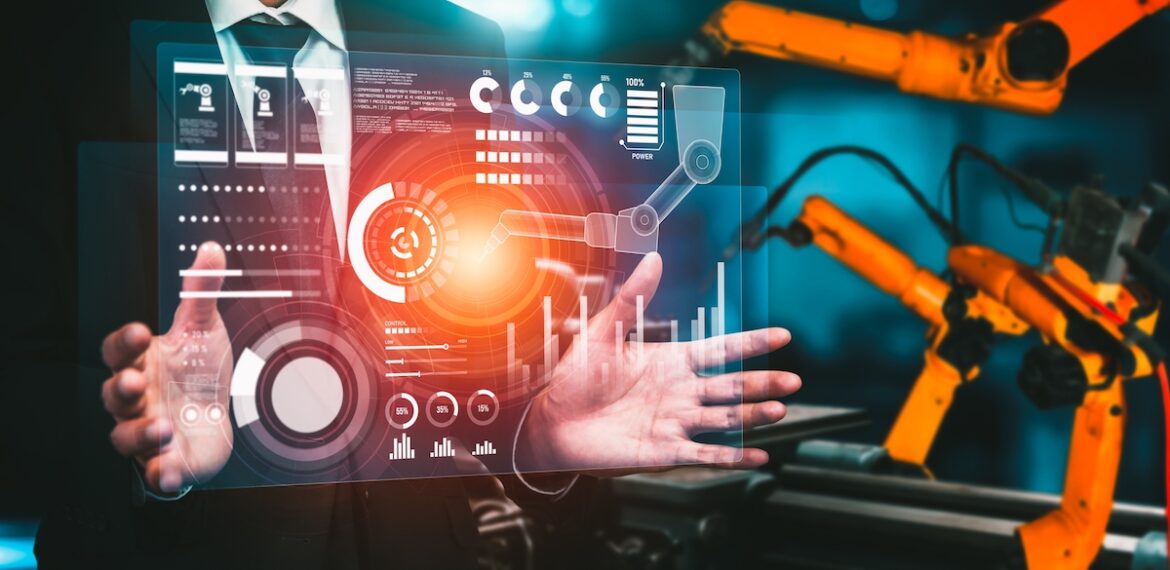
Use Cases Series – 5 – Optimizing Manufacturing with Data Analytics
Use Cases Series – 5 – Optimizing Manufacturing with Data Analytics
In the relentless pursuit of efficiency, quality, and sustainability, the manufacturing sector is posed for a significant transformation, driven by the advent and integration of data analytics. As we navigate through an era marked by technological advancements and evolving market demands, the ability to harness the vast volumes of data generated across manufacturing processes has become a key determinant of success. Data analytics, with its promise to unearth hidden patterns, predict future trends, and optimize operations, is revolutionizing the manufacturing landscape. From enhancing machine uptime through predictive maintenance to refining quality control processes and optimizing supply chains, the applications of data analytics in manufacturing are vast and varied.
This blog delves into ten critical use cases where data analytics is not just improving operational efficiencies but is fundamentally transforming how manufacturers compete and thrive in today’s global market. By exploring these use cases, we aim to showcase how leveraging the power of data analytics is paving the way for a new era in manufacturing – one that is smarter, more responsive, and increasingly aligned with the demands of a digital world.
The Data-Driven Paradigm Use Cases for Manufacturing
1. Predictive Maintenance:
Predictive maintenance stands out as one of the most impactful applications of data analytics in manufacturing. By analyzing data from machine sensors and historical maintenance records, manufacturers can predict when equipment might fail and perform maintenance proactively. This approach not only minimizes downtime but also extends the lifespan of machinery, significantly reducing maintenance costs and improving production efficiency.
2. Quality Control and Assurance:
Data analytics revolutionizes quality control processes by enabling real-time monitoring and analysis of product quality against set standards. By identifying deviations in the production process that could lead to defects, manufacturers can take immediate corrective actions. This real-time insight helps maintain high-quality standards, reduces waste, and ensures customer satisfaction.
3. Supply Chain Optimization:
In the complex web of modern supply chains, data analytics offers unprecedented visibility and control. Analyzing data from various points in the supply chain, including supplier performance, logistics, and inventory levels, allows manufacturers to identify bottlenecks, predict future disruptions, and optimize inventory management. This results in more resilient supply chains, reduced costs, and improved delivery times.
4. Energy Consumption Analysis:
Manufacturers are increasingly focusing on sustainability and cost reduction by optimizing energy usage. Data analytics enables the analysis of energy consumption patterns across different processes and identifies areas where energy use can be reduced without impacting production. This not only lowers operational costs but also contributes to the environmental sustainability of manufacturing operations.
5. Product Lifecycle Management:
Data analytics enhances product lifecycle management by providing insights into every stage of a product’s life, from design and production to use and disposal. By analyzing customer feedback, usage data, and product performance, manufacturers can make informed decisions about product design improvements, potential recalls, or discontinuation, ensuring the product meets market needs and regulatory requirements.
6. Customization and Personalization:
The demand for customized and personalized products is growing, and data analytics allows manufacturers to meet these needs efficiently. By analyzing customer data and preferences, manufacturers can tailor production processes to create customized products at scale, enhancing customer satisfaction and opening new market opportunities.
7. Workforce Productivity and Safety:
Data analytics plays a critical role in enhancing workforce productivity and safety. By analyzing data from wearable devices, machinery, and environmental sensors, manufacturers can identify patterns that indicate potential safety risks or inefficiencies in workflows. This data-driven approach ensures a safer working environment and helps optimize labor allocation and productivity.
8. Market Demand Forecasting:
Accurate demand forecasting is crucial for efficient manufacturing operations. Data analytics enables manufacturers to analyze market trends, consumer behavior, and sales data to predict future product demand. This insight allows for better production planning, inventory management, and reduces the risk of overproduction or stockouts.
9. Operational Efficiency and Process Optimization:
Data analytics offers manufacturers the tools to achieve operational excellence. By continuously monitoring and analyzing production data, manufacturers can identify inefficiencies, streamline processes, and implement lean manufacturing principles. This leads to improved operational efficiency, reduced costs, and higher profit margins.
10. Innovation and Product Development:
Finally, data analytics fuels innovation and product development in manufacturing. By leveraging data from market research, customer feedback, and competitive analysis, manufacturers can identify emerging trends and customer needs. This insight drives the development of new products and services, ensuring that manufacturers remain competitive in a fast-evolving market.
Future Trends in Data Analytics for Manufacturing
The future of manufacturing is set to be transformed by a wave of advancements in data analytics, blending technology with strategic insights to drive efficiency, innovation, and sustainability. Here are five consolidated trends that encapsulate the future trajectory of data analytics in the manufacturing sector:
1. Advanced AI Integration and Real-time Processing:
The fusion of Artificial Intelligence (AI) and Machine Learning (ML) with real-time data processing technologies, such as edge computing, is poised to redefine manufacturing operations. This trend will enable not only sophisticated predictive analytics for maintenance and production optimization but also facilitate immediate decision-making at the production line level. The ability to process data on-site, close to where it’s generated, will minimize delays, enhancing operational responsiveness to market demands and production anomalies.
2. Digital Twins and Augmented Reality for Operational Excellence:
Digital twin technology, complemented by Augmented Reality (AR), is set to revolutionize product development, maintenance, and employee training. By creating virtual replicas of physical systems, manufacturers can simulate and analyze operations, predict outcomes, and plan for the future with unprecedented accuracy. AR brings these insights into the real world, providing workers with real-time, actionable data overlaid on their physical environment, thus improving maintenance procedures and accelerating the learning curve for new employees.
3. Blockchain-Enhanced Supply Chain Transparency and Cybersecurity:
Blockchain technology will emerge as a key player in enhancing supply chain transparency and cybersecurity within the manufacturing sector. Offering a secure, transparent ledger for recording transactions, blockchain will improve traceability, reduce counterfeiting, and foster trust between manufacturers and suppliers. Additionally, as the Internet of Things (IoT) devices become more prevalent in manufacturing, blockchain will play a crucial role in safeguarding data integrity and preventing cyber threats.
4. Sustainability Analytics and Customization at Scale:
Driven by global environmental concerns and consumer demand for personalized products, manufacturers will increasingly rely on data analytics for sustainability tracking and mass customization. Sustainability analytics will monitor and optimize energy use, emissions, and resource consumption, aligning manufacturing practices with environmental goals. Simultaneously, analytics will enable manufacturers to efficiently tailor products to individual consumer preferences, achieving customization at scale without compromising production efficiency.
5. Collaborative Automation and Market Predictive Analytics:
The integration of collaborative robots (cobots) and automated systems, powered by data analytics, will enhance human-machine collaboration, optimizing production lines and performing tasks with precision and flexibility. In parallel, predictive analytics will provide manufacturers with foresight into market trends and consumer behaviors, allowing them to proactively adjust their strategies and maintain a competitive edge in rapidly changing markets.
Challenges and Considerations in Implementing Data Analytics in Manufacturing
The adoption of data analytics in manufacturing heralds a transformative era of efficiency and innovation. However, navigating the integration of these technologies presents a unique set of challenges and considerations. Addressing these issues is crucial for manufacturers to fully harness the potential of data analytics and mitigate any associated risks.
1. Data Quality and Integration:
One of the fundamental challenges in leveraging data analytics is ensuring the quality and integration of data from diverse sources. Manufacturing operations often involve a myriad of machines, sensors, and systems, each generating vast amounts of data in different formats. Integrating this data into a cohesive, analyzable format is critical. Poor data quality or inconsistent data integration can lead to inaccurate analyses, potentially leading to flawed decision-making processes.
2. Skills Gap and Workforce Training:
As manufacturing becomes increasingly reliant on data analytics, a significant skills gap has emerged. The demand for data scientists, analysts, and technicians who can interpret and act on data insights exceeds the current supply. Moreover, existing employees may lack the necessary skills to leverage new data-driven tools and technologies. Addressing this gap through comprehensive training programs and partnerships with educational institutions is vital for the successful implementation of data analytics.
3. Cybersecurity and Data Privacy:
The integration of data analytics in manufacturing operations increases the risk of cyber threats and data breaches. With more devices connected to the Internet of Things (IoT) and an increasing amount of sensitive data being processed, manufacturers must prioritize cybersecurity measures. Protecting data privacy, especially in regions with strict data protection regulations, adds another layer of complexity to data analytics implementation.
4. Cost and ROI Concerns:
Implementing data analytics infrastructure can require significant upfront investment in technology, training, and process redesign. For many manufacturers, especially small and medium-sized enterprises (SMEs), these costs can be prohibitive. Moreover, demonstrating a clear return on investment (ROI) is crucial for justifying these expenses. Manufacturers must carefully assess the potential benefits of data analytics against the costs, considering both short-term impacts and long-term strategic advantages.
5. Cultural and Organizational Resistance:
The shift towards data-driven manufacturing can encounter cultural and organizational resistance. Changing long-standing processes and adopting new technologies can be met with skepticism from employees accustomed to traditional methods. Overcoming this resistance requires strong leadership, clear communication of the benefits of data analytics, and the involvement of employees at all levels in the transition process.
Conclusion
In reflecting on the transformative potential of data analytics within the manufacturing sector, it’s evident that this technological evolution is not just enhancing current operations but also charting a course towards a future where efficiency, innovation, and responsiveness define industry standards. The exploration of data analytics use cases, from predictive maintenance to supply chain optimization and beyond, underscores the vast array of opportunities for manufacturers to leverage data for strategic advantage. As the industry continues to embrace these data-driven approaches, the promise of achieving higher operational efficiency, reduced costs, and a competitive edge in the market becomes increasingly tangible. The journey towards integrating data analytics into manufacturing processes heralds a new era of industrial productivity and innovation, where data becomes the linchpin of decision-making and strategic planning.
However, this journey is also accompanied by its share of challenges and considerations, including the imperative of ensuring data privacy and security, overcoming technical and infrastructural hurdles, and navigating the complexities of regulatory compliance. The future trends in data analytics for manufacturing point towards a landscape rich with potential but also fraught with the need for vigilance, adaptability, and ethical consideration. As manufacturers navigate this evolving terrain, the focus must remain on harnessing the power of data analytics responsibly and sustainably, ensuring that technological advancements contribute not only to the bottom line but also to the broader goals of environmental stewardship and societal well-being. In doing so, the manufacturing industry can fully realize the promise of data analytics, driving forward into a future marked by resilience, efficiency, and continuous innovation.
Let Datahub Analytics be your guide in unlocking the full potential of data analytics, ensuring your place as a leader in the new era of manufacturing.
We stand at the forefront of integrating data analytics into manufacturing processes, offering tailored solutions that harness the power of data to unlock unprecedented efficiency, innovation, and competitive advantage for our clients. Our cutting-edge analytics platforms and expert consultancy services are designed to navigate the complexities of modern manufacturing, from optimizing supply chains to predictive maintenance, quality control, and beyond. We understand the unique challenges manufacturers face, including data security, integration, and scalability. Our commitment is to not only address these challenges but also to transform them into opportunities for growth and innovation.
Partnering with us means embarking on a journey towards a data-driven future, where informed decision-making and strategic insights pave the way for operational excellence and sustainable success in the ever-evolving manufacturing landscape.